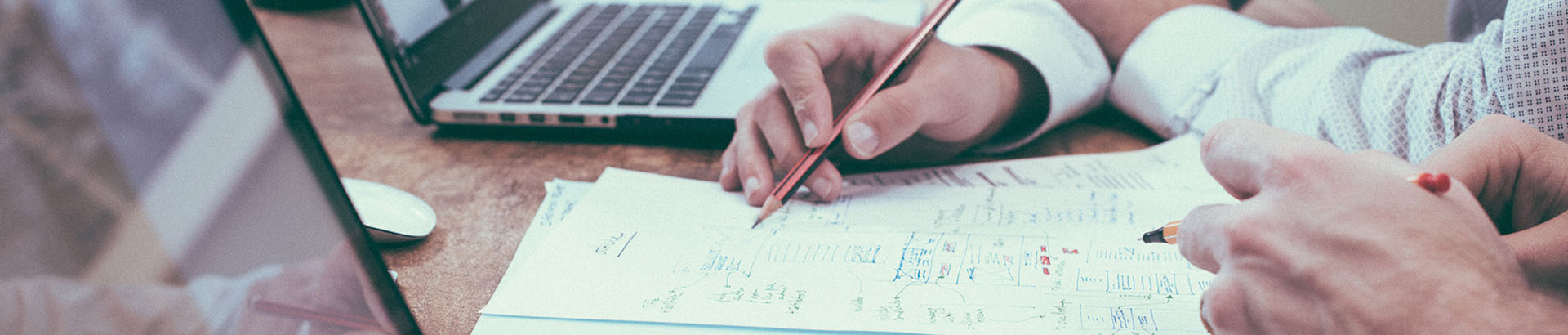
CASE STUDY

Organisational development
Situation
New environmental implications and increased competition both from existing European firms and a new global player force the group to optimise operational costs, including staff cost.
Production facility consists of 1000+ employees and three different entities. Downsizing was the main target for saving cost and achieving competitive advantage compared to others in the core market.
Production facility consists of 1000+ employees and three different entities. Downsizing was the main target for saving cost and achieving competitive advantage compared to others in the core market.
Complication
Except for the desire to significantly reduce operational costs, no further direction was given by the client:
- No clear target communicated to managers
- Industry benchmarks not accepted/supported
- Lack of resources for intensive process redesign
- Protectionism of certain business areas
- Lack of motivational culture to enforce strong company belongingness and pride
Solution
Through a step-by-step bottom-up approach, all the existing positions were challenged, discussed and analysed using a clear methodology. Achievements were brought through:
- Reduction of outright and backup positions
- Conducting job aggregation jointly with cross-training
- Identifying reduction potential after investments and modernisation
- Freeing up management time by redistributing responsibility
Example
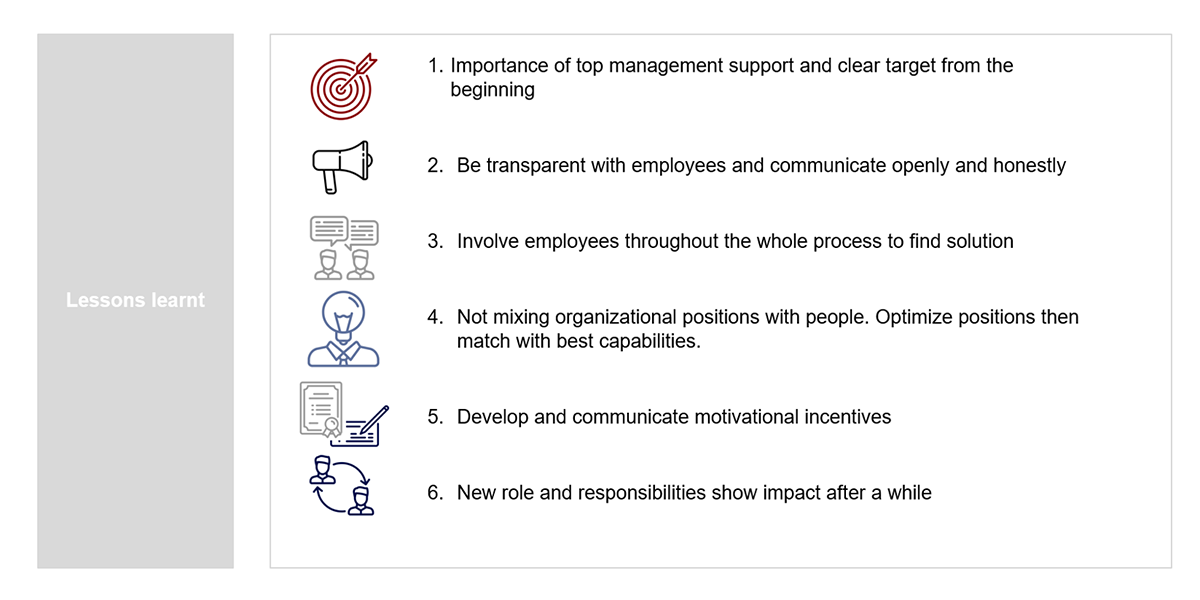